Support Center
The Yamaha Quality Support Center
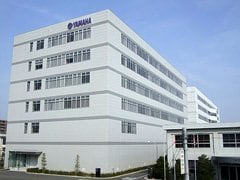
Right near the entrance to one of Yamaha's main office and factory complexes stands an imposing, almost windowless structure that is a vital arm of Yamaha's Quality Management System. The Quality Support Center is a world-class testing laboratory that houses some of the most advanced and sensitive testing facilities for electronic devices available anywhere, plus some tortuous durability tests that are almost shocking in their severity. The EMC test chambers at the Quality Support Center comply with ISO 17025 standards: "general requirements for competence of testing and calibration laboratories." Not many manufacturers operate an internationally accredited facility of this scale or capability.
Electromagnetic Compatibility
The Yamaha Quality Support Center houses a number of state-of-the-art electromagnetic compatibility testing chambers of various sizes. This is where all electronic products are rigorously tested for electronic interference and susceptibility. A product may visit the facility several times during development until the required level of EMC performance is achieved.
Large EMC Test Chamber
EMC Test Chamber Control Room
Small EMC Test Chamber
Parts Testing
Individual parts that are to be used in Yamaha products are thoroughly tested to ensure that they meet performance specifications, and that they will maintain their performance through extended, repeated use. Mechanical parts such as controls and faders are subject to particularly stringent tests. Control samples must undergo tens of thousands of operating cycles without failure before they are approved for use in Yamaha products. Even cables are subject to extensive flexion testing under load. Parts that can be damaged if physically opened are examined using advanced non-destructive x-ray tomography techniques, and many parts and finishes are carefully tested for potentially hazardous VOC (volatile organic compound) emission. There's more, but this abbreviated list should give you an idea of the degree of the detail and depth of the testing that is required for each and every Yamaha product.
Encoder Durability Testing
Non-destructive X-ray Tomography
Cable Durability Testing
Drop and Vibration Testing
Products must reach the customer in perfect working order, so packaging and shock resistance are important quality issues.
Testing is brutally simple: drop the product from a specified height (onto corners as well as top, bottom, and sides), and subject it to severe mechanical vibration covering a range of frequencies for extended periods. If the product and packaging can survive Yamaha's internal testing, they can survive transportation around globe under the roughest conditions.
Computer-controlled Vibration Table
Small-item Drop Test
Yamaha Quality Control: Quality Management
Yamaha's Quality & Engineering Planning Division handles testing requested by the various product development divisions in accordance with the Yamaha Quality Management System.
Production
Production can only begin after the final engineering samples have passed all tests and have been fully approved by the Quality Support Center as well as all of the involved development groups. But that is by no means the end of quality management. Monitoring and testing continue throughout the manufacturing process to ensure that quality goals are maintained.